Introduction
Additive printing, commonly known as 3D printing, is revolutionizing how we design, prototype, and manufacture products. Unlike traditional subtractive methods (cutting, drilling, or machining), additive manufacturing builds objects layer by layer, offering unprecedented design freedom, cost efficiency, and customization.
From aerospace components to custom medical implants, industries worldwide are adopting this technology to accelerate production, reduce waste, and innovate faster. In this guide, we’ll explore:
✅ What additive printing is and how it works
✅ Key technologies (FDM, SLA, SLS, Metal 3D Printing)
✅ Industries being transformed
✅ Benefits and challenges
✅ The future of additive manufacturing
Let’s dive in!
What Is Additive Printing?
Additive printing is a digital fabrication process where a 3D object is created by adding material layer upon layer, based on a computer-aided design (CAD) model. This contrasts with subtractive manufacturing (e.g., CNC machining), where material is removed from a solid block.
A Brief History
- 1980s – The first 3D printing technology (Stereolithography/SLA) was invented by Chuck Hull.
- 1990s – Fused Deposition Modeling (FDM) and Selective Laser Sintering (SLS) emerged.
- 2010s – Metal 3D printing became viable for aerospace and medical use.
- Today – Additive printing is used for everything from car parts to human organs.
How Does Additive Printing Work?
The process involves three main steps:
- Design – A 3D model is created using CAD software (e.g., SolidWorks, Fusion 360).
- Slicing – Specialized software (e.g., Cura, PrusaSlicer) divides the model into thin layers.
- Printing – The 3D printer builds the object layer by layer using materials like plastic, resin, or metal.
Key Additive Printing Technologies
Technology | How It Works | Best For |
---|---|---|
FDM (Fused Deposition Modeling) | Melts plastic filament and extrudes it layer by layer | Prototyping, hobbyists, low-cost parts |
SLA (Stereolithography) | Uses UV laser to harden liquid resin | High-detail models, dental & jewelry |
SLS (Selective Laser Sintering) | Laser fuses powdered material (plastic/metal) | Industrial parts, functional prototypes |
DMLS (Direct Metal Laser Sintering) | Laser melts metal powder for aerospace/medical | Strong, complex metal components |
Key Benefits of Additive Printing
1. Design Freedom & Complexity
- Enables intricate geometries (hollow structures, lattices) impossible with traditional methods.
- Example: Lightweight aerospace parts with internal cooling channels.
2. Rapid Prototyping & Faster Time-to-Market
- Companies like Tesla and Boeing use 3D printing to test designs in days, not months.
3. Cost Efficiency & Less Waste
- No need for expensive molds – Ideal for small-batch production.
- Up to 90% less material waste vs. CNC machining.
4. Customization & Personalization
- Medical: Tailored prosthetics, dental aligners (Invisalign).
- Fashion: Custom-fit shoes (Adidas 4D) and jewelry.
5. Sustainability
- Reduces carbon footprint by minimizing material waste and transportation.
Industries Transformed by Additive Printing
🏢 Aerospace & Defense
- NASA & SpaceX use metal 3D printing for rocket engines.
- GE Aviation prints fuel nozzles, cutting weight by 25%.
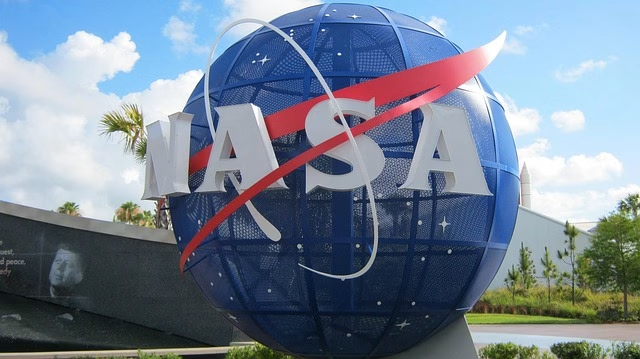
🏥 Healthcare & Bioprinting
- Custom implants (titanium skull plates, hip replacements).
- Bioprinting research – Lab-grown organs using living cells.
🚗 Automotive
- BMW & Ford 3D print spare parts and lightweight components.
- Local Motors created the world’s first 3D-printed car (Strati).
🏗️ Construction
- 3D-printed houses (completed in 24 hours for under $10K).
Challenges & Limitations
❌ Not Ideal for Mass Production – Slower than injection molding for large volumes.
❌ Material Constraints – Limited high-strength polymers/metals.
❌ Post-Processing Required – Often needs sanding, polishing, or heat treatment.
❌ High Initial Costs – Industrial machines can cost $100K+.
The Future of Additive (3D) Printing
🔮 AI-Driven Design – Generative AI optimizes structures for strength/weight.
🔮 Multi-Material Printing – Combining metals, plastics, and electronics.
🔮 Large-Scale Construction – 3D-printed skyscrapers and bridges.
🔮 Bioprinting Breakthroughs – Functional organs for transplants.
Conclusion
Additive printing reshapes manufacturing, offering unmatched flexibility, speed, and sustainability. While challenges remain, advancements in materials, AI, and automation are pushing the boundaries of what’s possible.
🚀 Ready to explore additive or 3D printing? At Tridimensio, we provide cutting-edge 3D printing solutions for businesses and innovators. Contact us today to learn more!
FAQ Section
Q: Is additive printing the same as 3D printing?
A: Yes! “Additive printing” is the industrial term, while “3D printing” is more common in consumer markets.
Q: What materials can be used?
A: Plastics (PLA, ABS), resins, metals (titanium, aluminum), ceramics, and even bio-inks.
Q: How accurate is additive printing?
A: Depending on the technology, precision ranges from ±0.1mm (SLA) to ±0.5mm (FDM).