Introduction: The Rise of Rubber-Like 3D Printing
In a BMW factory in Munich, engineers now 3D print custom TPU gaskets directly onto assembly robots. Meanwhile, at Stanford’s Biodesign Lab, researchers are printing TPU heart valves that mimic human tissue elasticity. This is the new reality of thermoplastic polyurethane (TPU) printing – a technology bridging the gap between industrial manufacturing and biological innovation.
What Makes TPU Unique?
TPU (Thermoplastic Polyurethane) stands out in 3D printing for its:
✅ Flexibility: Ranges from Shore 60A (squishy) to 85D (semi-rigid)
✅ Durability: Withstands 500%+ elongation without tearing
✅ Chemical Resistance: Oil, grease, and solvent-resistant
✅ Layer Adhesion: Excellent interlayer bonding
“TPU is the Goldilocks material – not too hard, not too soft, but just right for functional prototypes,” says Dr. Emily Parker, Materials Engineer at Stratasys.
Top 5 TPU Printing Applications in 2025
1. Automotive Components
- Vibration-damping mounts (30% lighter than rubber)
- Custom weather stripping (printed on-demand at dealerships)
- Airless tires (Michelin’s Uptis prototype)
Case Study: Porsche now prints TPU seat cushions tailored to driver body scans.
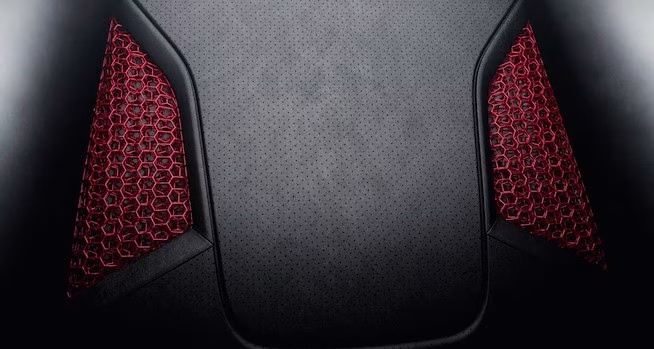
2. Medical Devices
- Orthotic insoles (98% patient comfort rating)
- Prosthetic liners (Reduces skin breakdown by 40%)
- Surgical guides (Sterilizable, flexible fit)
“TPU’s biocompatibility makes it ideal for patient-contact devices,” notes Dr. Raj Patel, FDA medical device reviewer.
3. Wearable Technology
Product | TPU Advantage |
---|---|
Smartwatch bands | Hypoallergenic, sweat-resistant |
AR/VR haptic gloves | Realistic texture simulation |
Athletic braces | Dynamic support during motion |
4. Industrial Robotics
- Gripper pads (Non-marking, high-friction)
- Cable management (Flexible printed conduits)
- Impact absorption (Damping elements for robotic arms)
5. Consumer Products
- Phone cases (15m drop protection)
- Shoe midsoles (Adidas 4DFWD uses TPU lattice)
- Waterproof seals (Replacing traditional gaskets)
How to Successfully Print with TPU
Printer Requirements
✔ Direct Drive extruder (Bowden tubes cause issues)
✔ Enclosure (for temperature stability)
✔ Heated bed (60-80°C recommended)
Optimal Settings
Parameter | Value Range |
---|---|
Nozzle Temp | 220-250°C |
Bed Temp | 60-80°C |
Print Speed | 20-40 mm/s |
Retraction | 1-2mm (minimal) |
Cooling | 30-50% fan |
Pro Tip: Use glue stick or PEI sheet for bed adhesion – TPU loves to stick too well!
TPU vs. Other Flexible Filaments
Material | Shore Hardness | Elongation | Best For |
---|---|---|---|
TPU | 60A-85D | 500%+ | Functional parts |
TPE | 30A-70A | 800%+ | Ultra-flexible items |
TPEE | 40D-72D | 300% | Repeated flexing |
PLA Flexible | 90A-95A | 200% | Beginner projects |
“TPU hits the sweet spot between flexibility and printability,” explains Thomas Sandmeier, CEO of Filamentive.
Emerging TPU Innovations
- Conductive TPU (for printed sensors)
- Self-healing TPU (microcapsule technology)
- Color-changing TPU (thermochromic additives)
- Foam TPU (60% weight reduction)
Industry Forecast: The TPU filament market will grow at 14.7% CAGR through 2029 (Grand View Research).
Common TPU Printing Challenges & Solutions
Problem: Stringing/Oozing
Fix:
- Reduce nozzle temp by 5-10°C
- Enable coasting in slicer
- Use wipe settings
Problem: Poor Layer Adhesion
Fix:
- Increase extrusion width to 120%
- Slow print speed to 30mm/s
- Disable cooling for first 5 layers
Problem: Bed Adhesion Too Strong
Fix:
- Use removable build surfaces
- Apply diluted IPA as release agent
- Wait for bed to cool below 35°C
FAQ: TPU Printing Essentials
Q: Can I print TPU on any 3D printer?
A: Only with direct drive extruders. Bowden setups typically fail.
Q: Is TPU waterproof?
A: Yes – it’s ideal for marine applications when printed at 100% infill.
Q: How flexible is 95A vs. 85A TPU?
A: 85A bends like a rubber eraser; 95A feels like a stiff shoe sole.
Q: Does TPU need drying before printing?
A: Absolutely – 4-6 hours at 60°C prevents bubbling.